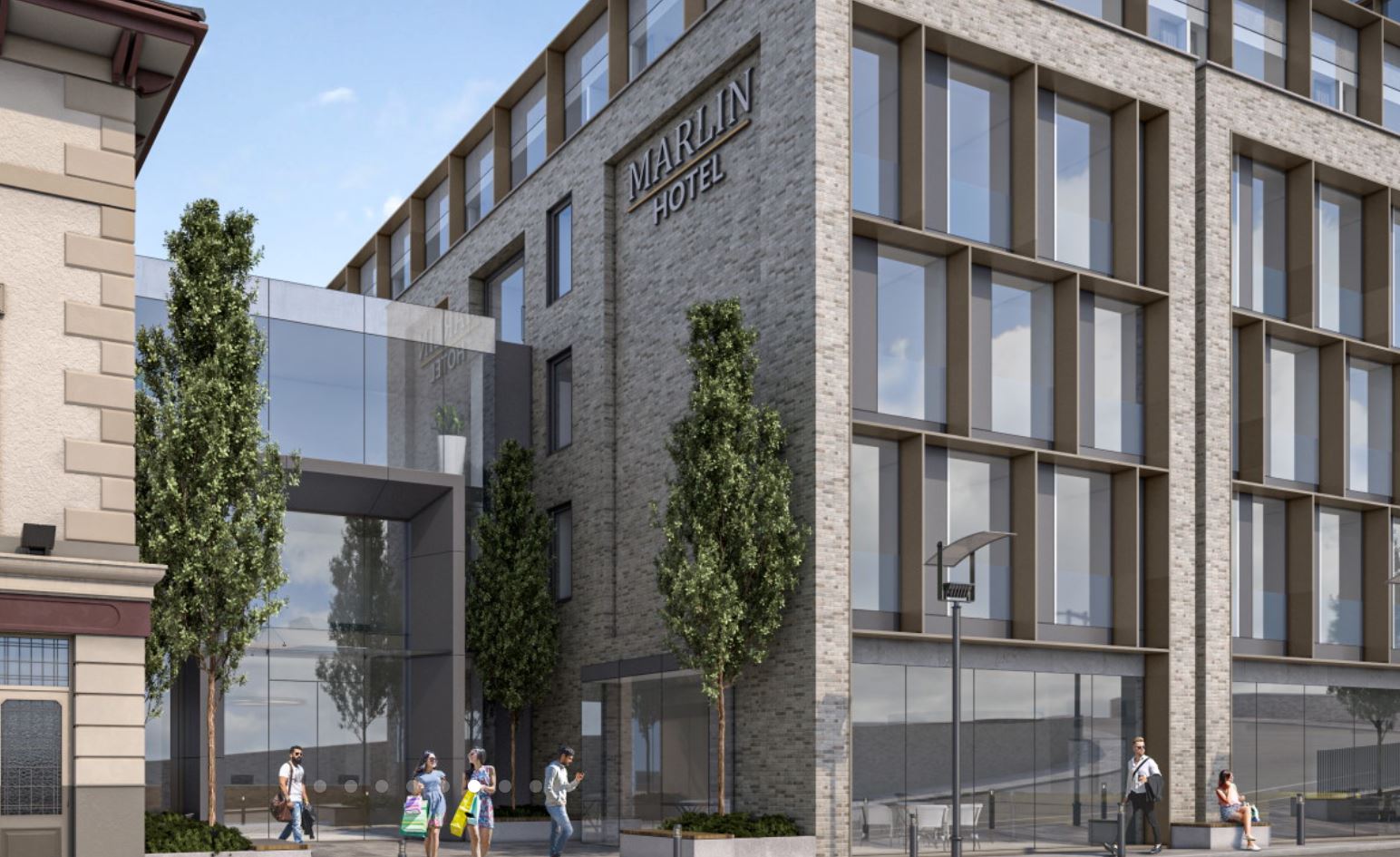
What are the 7 Categories of MMC?
In an era where efficiency, sustainability, and innovation are more than just buzzwords, understanding MMC is crucial for anyone involved in the building and design industry.
From architects and developers to investors and homeowners, these methods are reshaping how we think about and execute construction projects, and with every advancement in technology these methods are becoming widespread and accessible.
Here at Studio Anyo, we are proud to be at the forefront of the MMC revolution, and these methods have been right at the heart of our growth as a sustainable, forward-thinking architecture brand.
In this blog, we’ll unravel the seven distinct categories of MMC, shedding light on how each one is contributing to a revolution in the construction sector.
Let’s take a look.
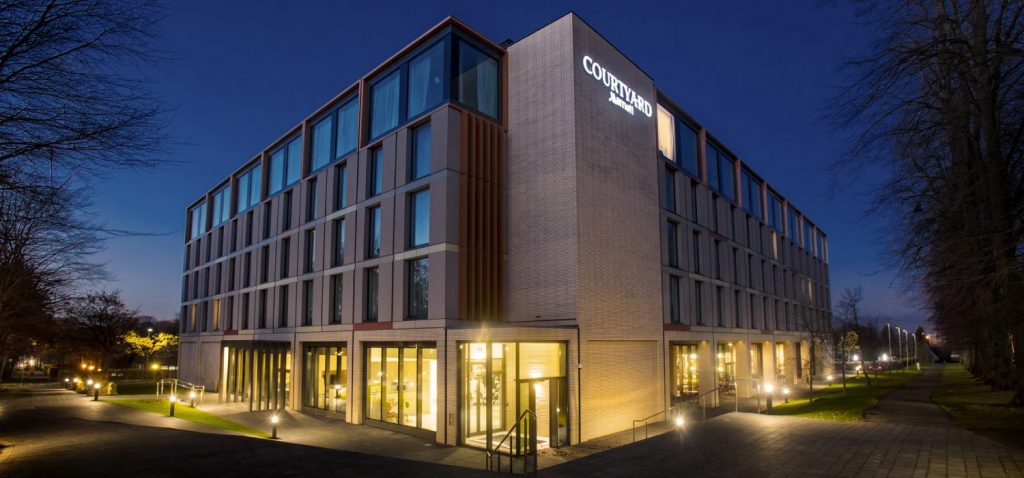
The 7 Categories of MMC
As we delve into the intricacies of Modern Methods of Construction (MMC), it’s essential to understand the diverse range of approaches encompassed within this innovative field.
The construction industry, always at the forefront of integrating technology and efficiency, has evolved dramatically, giving rise to MMC.
This evolution is categorised into seven distinct methods, each representing a unique approach to building and design.
These categories are not just classifications; they are a testament to the industry’s commitment to innovation, sustainability, and adaptability.
Here’s a brief overview of each category as defined by the British Government:
1. Pre-Manufacturing – 3D primary structural systems
This involves constructing three-dimensional units in a factory setting, which are then transported to the site for assembly.
These modules can be fully finished, with internal fittings and services installed, before they even reach the site for ultimate efficiency and to reduce the time spent on-site.
2. Pre-Manufacturing – 2D primary structural systems
These are flat panels that are manufactured off-site and assembled on-site to form a building.
They can be used for walls, floors, and roofs and are typically made from materials like timber, steel, or concrete.
The panels can be insulated (like Structural Insulated Panels, or SIPs) or non-insulated.
3. Pre-Manufacturing – Non-systemised structural components
This category combines elements of both volumetric and panelised systems.
Hybrid systems offer the flexibility of panelised systems with the speed of volumetric construction, allowing for more complex designs and layouts.
4. Pre-Manufacturing – Additive Manufacturing
Commonly known as 3D printing, this involves the use of digital 3D models to fabricate building components or even entire buildings by layering material.
This method offers high levels of customization and can significantly reduce waste.
5. Pre-Manufacturing – Non-structural assemblies and sub-assemblies
PMV refers to the value of off-site manufactured elements in a construction project.
This category is more about the economic aspect of MMC, focusing on how much of the project’s value is derived from pre-manufactured components.
6. Traditional building product led site labour reduction/productivity improvements
This includes traditional building methods but using modern materials and techniques to improve performance.
It’s about applying contemporary knowledge and practices to conventional construction approaches.
7. Site process led labour reduction/productivity improvements
This category involves innovative techniques applied on-site.
These could include novel methods of site preparation, innovative building techniques, or the use of modern, high-performance materials.
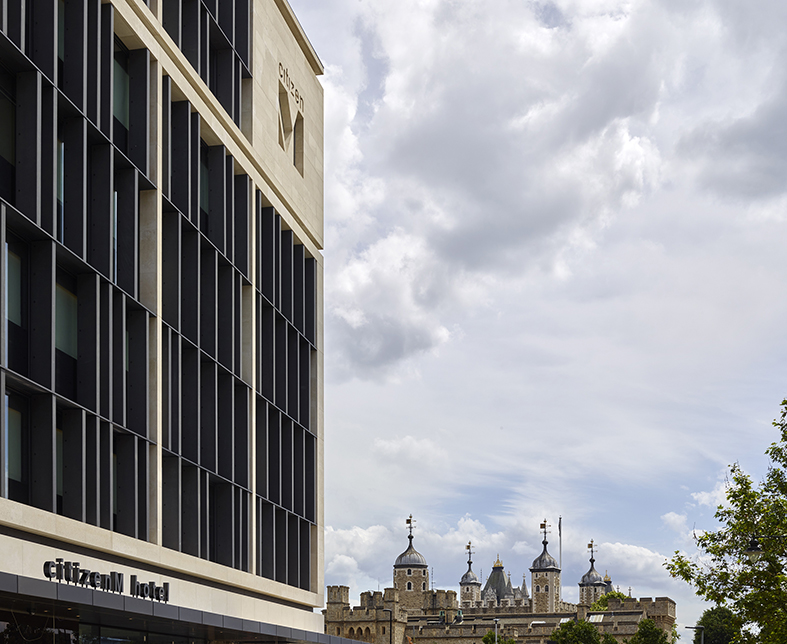
Why do the 7 categories of MMC exist?
The categories of Modern Methods of Construction (MMC) exist for several important reasons:
- Standardisation and Clarity: By categorising different construction methods, the industry can standardise terminology and concepts. This clarity is vital for communication among architects, builders, developers, and other stakeholders. It ensures everyone is on the same page regarding the techniques and processes being discussed or utilised.
- Specialisation and Expertise Development: Different categories allow professionals to specialise in specific methods. This specialisation leads to deeper expertise and more efficient and effective use of each method, enhancing overall quality and innovation in construction.
- Regulatory and Compliance Frameworks: Different construction methods may have varying regulatory requirements. Categorisation helps in creating specific compliance and safety standards tailored to each method, thereby ensuring safe and sustainable building practices.
- Facilitating Innovation and Adaptation: The construction industry is evolving rapidly, with new technologies and materials constantly emerging. Categorising MMC methods helps the industry to adapt to and integrate new innovations more effectively, keeping pace with advancements and market demands.
- Market Understanding and Investment: For investors and clients, understanding the different categories of MMC helps in making informed decisions about projects. It allows for a clearer assessment of the risks, benefits, and suitability of different construction methods for specific projects.
- Education and Training: Categories provide a framework for education and training programs. They help in structuring learning modules and professional development courses, ensuring that practitioners are well-versed in the latest methods and technologies.
- Sustainability and Efficiency Goals: Different MMC methods offer various sustainability and efficiency benefits. By categorising these methods, the industry can better target specific environmental goals, like reducing waste, lowering carbon emissions, or improving energy efficiency in buildings.
Overall, these categories help in organizing the vast array of construction techniques available today, fostering a more efficient, innovative, and responsive construction industry.
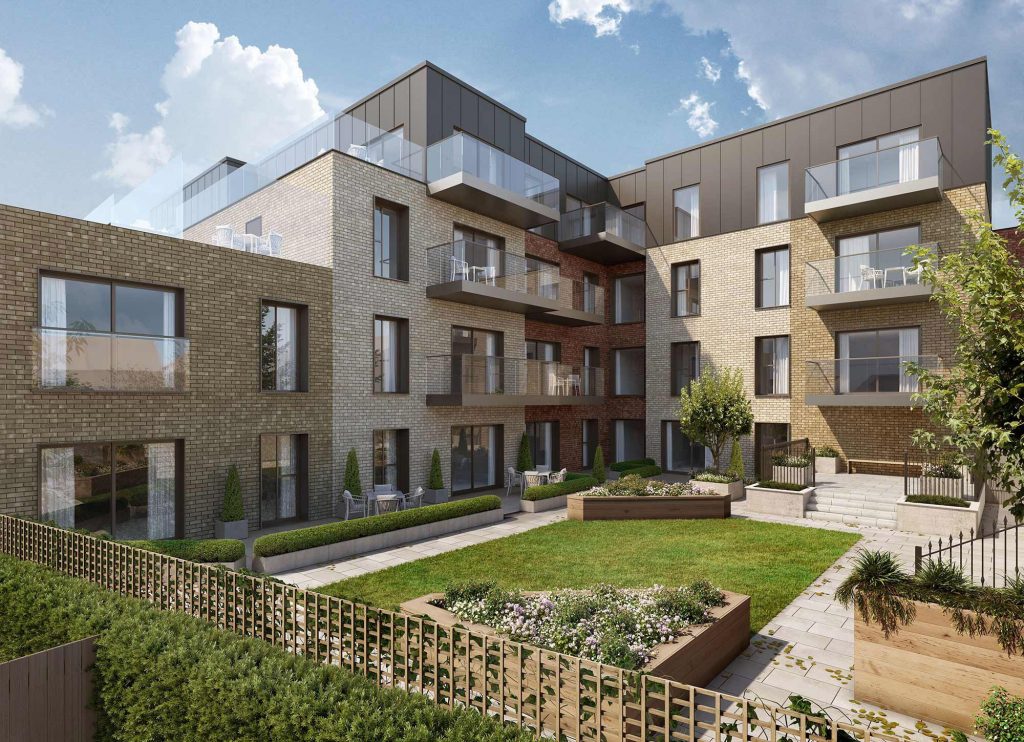
Studio Anyo: MMC Architects
As we’ve journeyed through the diverse landscape of Modern Methods of Construction, it’s clear that the future of building is not just about bricks and mortar. It’s about innovation, efficiency, and sustainability.
The seven categories of MMC represent the cutting edge of construction technology, offering solutions that are tailor-made for the challenges of the 21st century.
For professionals and enthusiasts alike, staying abreast of these developments isn’t just advantageous—it’s essential.
As the construction world continues to evolve, MMC stands at the forefront, leading the way towards a smarter, greener, and more efficient future in building and design.
Here at Studio Anyo, we have used these tactics across many projects, in student residential, traditional residential, and much more.
This includes our work on projects such as Marlin Stratford, on which we were designated MMC advisors.
Want to know more? Then contact our team today.