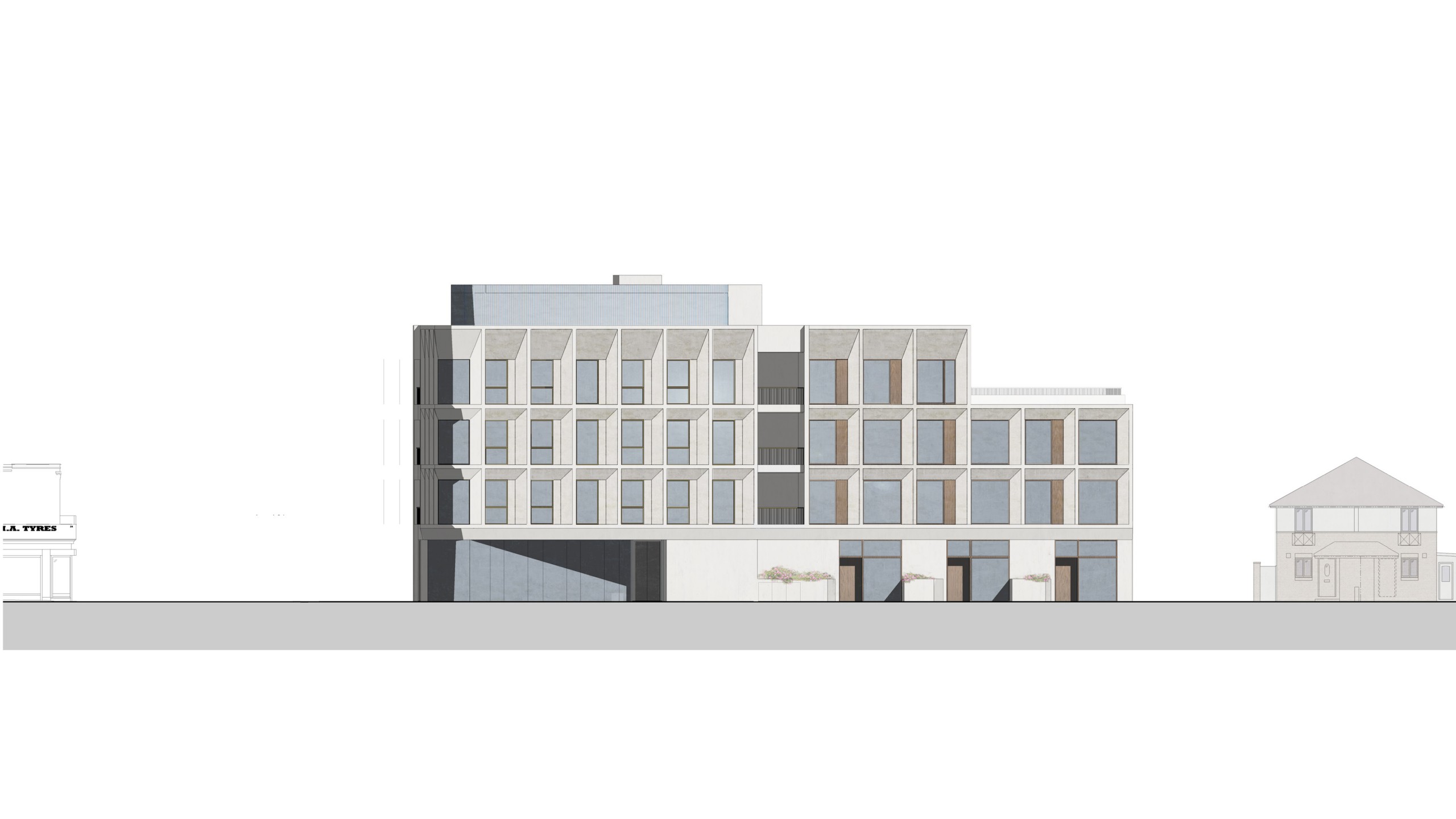
What is DFMA in Construction?
There are many different terms used in construction, but two that we focus on heavily here at Studio Anyo are MMC and DFMA.
The latter stands for Design for Manufacture and Assembly.
In a nutshell, this means using methods to optimise the design process of a building that will in turn lead to efficient and cost-effective manufacturing and assembly.
This is a term that may not be known very well outside of the construction industry, and therefore our team have compiled this guide on just what we mean when we say DFMA, and what methods fall under the bracket of this term.
Let’s take a look.
What Does DFMA Mean?
DFMA doesn’t involve just one process, but actually contains may varying methods.
At it’s essence, it is a way of making construction projects much more streamlined and reduces the time, labour, and cost it takes to complete these projects.
It involves analysing the design of a building and breaking it down into individual components and sub-assemblies.
Each component and sub-assembly is then evaluated for ease of manufacturing and assembly, as well as cost-effectiveness.
This evaluation process can help identify opportunities to simplify or streamline the design, reduce the number of components, and minimize the amount of labor required for construction.
DFMA is particularly important in modular construction, where buildings are constructed using prefabricated modules that are manufactured off-site and assembled on-site.
By optimizing the design for manufacturing and assembly, the construction process can be made more efficient and cost-effective, while still ensuring a high level of quality and safety.
What is the difference between DFMA and MMC?
While DFMA and MMC are both methods of optimising construction projects, there are some subtle differences which set the two apart.
MMC is a much broader term, and encompasses many more methods and stages of a construction project.
As mentioned earlier, DFMA focuses specifically on optimising the design of a building, and the end goal of DFMA is to simplify a design to such a level that there is less (or more simple) components and therefore will take less time and work to complete.
MMC covers much more than just the design phase and covers a whole range of construction techniques and processes that are designed to improve productivity and efficiency, including modular construction, off-site construction, and more.
MMC is focused on the full construction process, from start to finish, and not just on the design stage as DFMA is.
Some Common DFMA Techniques
There are several methods commonly practised under the umbrella of DFMA, and six of these are:
Standardisation
By standardising components and sub-assemblies, you are able to reduce the number of unique parts needed for the manufacture and construcution of a building. This is because you can use duplicate components, rather than having to design, produce, and construct unique ones every time. This is also a good way of simplifying the assembly process, as you can ensure standardised components fit together well and it won’t be too much trouble to construct a frame by combining them.
Modularisation
Dividing a building into modular components that can be manufactured off-site and then assembled on-site can reduce the need for on-site labour and speed up construction. It also makes it much easier to keep an eye on quality control and create components that you know are suitable to combine and the right fit for construction. This is often used for smaller buildings such as hotel pods, but can be used on larger structures.
Design for Assembly (DFA)
This involves designing components that are easy to assemble. For example, if you are needing to combine different components, using things such as self-aligning parts and snap-fit connections can streamline the entire assembly process. This is an important part of DFMA and is a key reason why using these methods can really optimise the construction process and reduce the risk of errors and need for amendments when the components are on-site.
Design for Manufacturing (DFM)
This is similar to DFA, but focuses on the manufacturing side of things. This means that every component is analysed and assessed to see if there are any ways that the manufacture of it can be simplified and streamlined. This can mean changing the shape of some components to something more simple, standardising dimensions so it is quicker to produce components, and making the requirements for extra work and equipment to be used minimal.
Design for Service (DFS)
Servicing components can be a time-consuming part of construction projects. For example, if all of the components you are using on-site require amendments or adjusting so that they fit together and are safe for use, then this will cost you time and money. DFS involves designing components and sub-assemblies that are easy to maintain and repair, reducing downtime and maintenance costs drastically.
Concurrent Engineering
Concurrent engineering is the process of involving all relevant stakeholders, including designers, manufacturers, and assemblers, in the design process to ensure that the design is optimized for all stages of the manufacturing and assembly process. This is a key part of DFMA as it helps you ensure all components are fit for the entire project and that it fits the vision and targets set by each individual workforce.
DFMA with Studio Anyo
If you are looking for advice, or a DFMA team to assist in your latest project, then why not head over to Studio Anyo.
Our team of architects, MMC advisors, and DFMA experts can assist your project in many ways, including working on the design process to optimise it using the methods listed above.
Want to know more?